Here are photos and descriptions of some of the instruments I have built. Many of these were designed by the buyers, while others were built to my specs
to sell "off the shelf".
Please see "Instruments For Sale" tab in the bar above for more information on available instruments.
![]() "Langeleik" SDD 0046My second custom "non-dulcimer." A woman from Colorado contacted me about building a "Langeleik" for her. These instruments are believed to be one of the older Norwegian influences that contributed to the design of the Mountain Dulcimer. It is basically a rectangular box strung with eight strings. Only one string is fretted while the other seven are played as "drone" strings. There are also included some small "movable" frets that can change the tuning of the drone strings like a capo. | ![]() Hourglass SDD 0014Aromatic cedar soundboard. Hard maple fingerboard. Scroll peghead. Orthodox cross soundholes. | ![]() Back View of Sdd 0014Hard maple back. Laminated peghead. | ![]() Hourglass SDD 0015Hourglass shape, hard maple fingerboard, aromatic cedar soundboard with "f" soundholes. Scroll peghead | ![]() Hourglass SDD 0016Aromatic cedar soundboard. Hickory fingerboard. Four different soundholes as selected by buyer. Custom carved peghead (whale tail fluke). | ![]() TEARDROP SDD 0018Teardrop shape, Sitka Spruce soundboard and Purpleheart fingerboard. Tapered scroll peghead. "f" soundholes. |
---|---|---|---|---|---|
![]() HOURGLASS SDD 0019Western Red Cedar soundboard on hourglass shaped body. Scroll peghead with down swept arch. Evergreen tree soundholes. Black walnut fingerboard with maple inlay dots. | ![]() Hourglass, SDD 0020Aromatic cedar soundboard, hickory fingerboard. Horsehead and geometric dot soundholes. Tapered scroll and upswept arch peghead. | ![]() Stand at first BazaarThe Spring Bazaar at the Evergreen fairgrounds in Monroe, our first event in 2015. | ![]() SDD 0022Aromatic cedar soundboard with Penguin soundholes. Laminated peghead. Gold tuning machines with black knobs. Special order Ebony fingerboard. | ![]() Hourglass, SDD 0025A couple of things to point out here. First notice the "Cannarywood" side on the body. This imported exotic hardwood has some beautiful grain patterns with colors ranging from browns to reds and oranges. Also the peghead has a different design. I was just experimenting while building it and ended up with something that reminded me of a turret on a castle. | ![]() Hourglass, SDD 0024Classic "hourglass" shape with leaf soundholes. Western Red Cedar soundboard and scroll type peghead. |
![]() Hourglass, SDD 0027Sides are one of my favorite exotic woods called Canarywood. Usually has multiple colored grain streaks ranging from very light to deep reds and even purples. Standard hourglass shape with Aromatic Cedar soundboard. "Bubble" soundholes. | ![]() Teardrop, SDD 0028Teardrop shape, stylish heart soundholes with dots above and below. Aromatic Cedar soundboard, | ![]() Diamond, SDD 0034Diamond body with matching soundholes. A tribute to some of the very early designs primarily from the Melton's of Virginia. Western Red Cedar soundboard, nicely grained Cherry back and sides. | ![]() Hourglass, SDD 0035Western Red Cedar on Hourglass shaped body. Padauk sides and back. Eight notes on upper "bout" and hearts on lower. | ![]() Rectangle, SDD 0037Rectangular body with rectangular soundholes produces a nice, clear sound. Built with contrasting colors to produce a light/dark theme. Soundboard is light colored Poplar. Sides are a dark Walnut and back is a bright Eastern Maple. | ![]() Hourglass, SDD 0039Fleur de Lis and Butterfly soundholes. Western Red Cedar sound board, Cherry back and Red Oak Sides. |
![]() Ellipse, SDD 0040Ellipse shaped, "f hole" soundholes. Soundboard is Red Alder, Backm is Black Walnut and sides are Cherry. | ![]() Hourglass, SDD 0043Four different soundholes on an hourglass shaped body. | ![]() Ellipse, SDD 0045Ellipise shape. | ![]() Hourglass, SDD 0047Hourglass. | ![]() 0051Certainly one of my top five favorite instruments. I found a piece of poplar that was "marred" by a dark stripe within the grain of the wood. After some creative book-matching and milling I ended up with a unique looking soundboard for this elliptical dulcimer. | ![]() Rectangle, SDD 0052Tribute to early builders that used whatever they could find for building materials. Sometimes they would use cigar boxes to construcg the body, creating an instrument with a rectangular shape like this one. |
![]() Ellipse, SDD 0053Eliptical shape with standing bear and howling wolf soundholes. | ![]() "Very Custom" SDD 0054Ordered by customer in Vermont. | ![]() Diamond, SDD 0055A little different view of a lesser used shape - diamond. | ![]() "Trumpet" Shape SDD 0061A bit of a different design that I tried out in an attempt to come up with a less expensive dulcimer. It was not a lot less to build but did evolve into another "Economy" model that I am now building. | ![]() Elliptical, SDD 0065Custom order instrument. Notice the laminated woods in the peg head. I enjoy doing this little extra touch and feel that it adds to the uniqueness of each instrument. | ![]() Teardrop, SDD 0067This soundboard is Aromatic Cedar, also known as Tennessee Cedar. While it has been a popular option with many of my customers, I am finding that good quality lumber of this species is getting hard to get. |
![]() Rectangle, SDD 0076Basic model with some upgrades. Soundboard is Western Red Cedar. | ![]() Hourglass, SDD 0077Hourglass shape, Crescent moon soundholes. | ![]() Teardrop SDD 0083 | ![]() Another commissioned Langeliek for a customer in North Dakota. SDD 0087 This is considered one of | ![]() SDD 0088, Hickory bookmatched back with laminated racing stripe adds a distinctive personal touch. | ![]() Peghear detail for SDD 0090. Laser edched initials or other items can also be added onto scroll typ |
DESIGN
SHAPES

These are miniature examples of the most common shapes I build. From left to right they are:
Hourglass: Probably the most popular yet still very traditional.
Aorell: The least seen nowadays and one of the more difficult to build.
Ellipse: Also not seen a lot but but produces a little richer tonal quality.
Teardrop: Second most popular after the hourglass. Light weight, bright sounding. Fewer soundhole
options due to size.
Cigar Box: Good value. Nice mellow tones. Reminiscent of when times were hard but the
resiliant people of Appalachia made do with what they had. A great reminder of
the "Good Ol' Days"
WOOD SPECIES
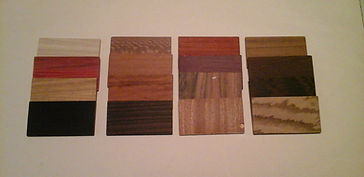
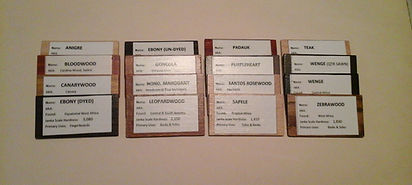

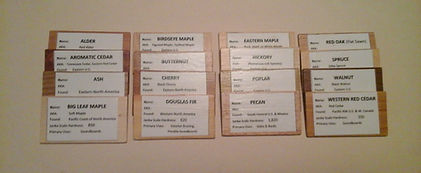
Some of my wood samples
Wood Species
Choosing the wood for an instrument entails much more than simply what you like the looks of. We have to consider factors such as what is available or how long it may take to get it. Price can be an issue as well. Some of the species I use can be a little as $2.30 per board foot while some imported exoctics I have special ordered for customers can be upwards of $150.00 per board foot.
Another consideration is the hardness of the wood. This is what determines how the insturment will sound when completed. Let's follow what happens when a dulcimer string is made to vibrate by plucking or strumming...
The vibrations are first imparted to the fretboard. This should be a medium density wood which will then carry the vibrations to the soundboard.
The soundboard needs to be a softer wood which will allow it to pick up the vibrations from the fretboard and amplify them.
The vibrations actually become amplified at this point. The sides and back of the dulcimer should be of a harder wood to act somewhat as an echo chamber to further resonate the sound waves.
The grain pattern of the wood is another important piece of the picture. We need tight, vertical grain wood for the soundboard whereas the back can have more visually pleasing and interesting grain patterns. For sides that need to be steam bent, certain grain orientation will be less strong than others.
I take these (and other) factors into consideration when I help someone design their instrument and when I build my pre-built models. I have used Western Red Cedar, Aromatic Cedar, Alaskan Yellow Cedar, Sitka Spruce, Coastal Redwood and Poplar for soundboards. Backs and sides have been made with numerous domestic as well as exotic hardwoods. Most commonly I have used Eastern Maple, Cherry, Oak, and Black Walnut as well as Leopardwood, Purpleheart, and Canarywood.
When I am shopping for my wood, I make every attempt I can to source it locally. I believe it is important to see and feel the board I am considering purchasing. This allow me to visualize how it will cut and glue. How the grain is oriented. I can even get a feel for how it will sound by holding and knocking on it in a certain way. On rare occasions I have ordered boards on-line when something I needed was not available local
Crescent
Comet Moon Stylish Heart
Traditional Cross Diamond
Heart
Soundholes can range from the very simple to very detailed. They are likewise priced according to their degree of difficulty in cutting them out. One pair of these six soundholes is included in the price of a basic instrument. I also have a selection of over 25 other patterns available for nominal increases in the base price, and I would be happy to discuss a more complex custom design.
Some soundholes are not practical simply due to their design being such that the soundboard is weakened to the point that it will most likely break. If this is the case I may be able to suggest small changes to make it more workable.
The soundholes are cut out after the soundboard has been rough sawn, resawn, bookmatched, glued, and planed to thickness. If something goes amiss in the soundhole cutting there is more lost than simply a goobered hole. Re-doing the soundboard means repeating hours of time and wood replacement cost. (my loss, not the customers) This is the reason some of the more intricate designs are more costly
SOUNDHOLES

TUNING MACHINES

On my first few instruments I built, I used straight friction type tuning machines. I wanted to replicate the look of the old tapered wooden tuning pegs and at the same time keep costs down. (Friction machines were less expensive)
It didn't take long to figure out why they were less expensive. They didn't work real well. Because they were not geared, the peg would turn the same distance the knob was turned. This meant that if your string was tuned to "A-flat" and you wanted to bring it up to an "A", you might turn the knob the least bit you could and suddenly find you just raised the note to "C". They might work better on instruments that didn't require as much string tension but using them on mountain dulcimers just didn't work. They would also come out of tune quite readily.
I now almost exclusively use Grover Ukelele, 14:1 ratio, geared, right angle tuners. These come in nickel or gold colors and can have black, white or nickel knobs. The 14 to 1 ratio allows you change the tuning in very small increments and holds the note for a very long time before it needs re-tuning. The nickel colored tuners are included in the base price while the gold colored ones currently are an additional $10.00 per instrument.
For the serious musician that demands a very high quality tuning machine, I do have sources available where I can get professional grade tuners. Some of these can add as much as $140.00 to the cost of the instrument.
PEGHEADS
When it comes to designing the peghead, there is a lot of room for personal preferences. I have researched a lot and I have yet to find any evidence of one design having an advantage over another from a technical aspect. Also in talking with other dulcimer builders and players, the general consensus seems to be that the peghead is where you can be most creative. Here you can truely "have it your way".
Having said that, keep in mind that my goal in this whole project is to promote the heritage and history of the mountain music of the eastern United States. To that end I definitely lean towards the more traditional designs with only a little modernization thrown in to perhaps better accomodate tuning or stringing.
Most of my pegheads are either a "Scroll" design or a flat "Guitar" type. The true scroll design found on good violins and their cousins are very labor intense to carve. To keep the price of my instruments reasonable I instead use the very basic shape of a scrollhead and then dress it up with either grooves, tapering, or laminating different colored woods to give it some visual appeal.
The guitar type is pretty basic. I have used a few different shapes but here again I would rather keep them on the traditional side rather than a modernistic design.
If a you are interested in a custom design, and if I feel I can accomplish it in a reasonable amount of time I would be happy to discuss it with you.
The price of the Basic Instrument includes a choice of a number of different "Guitar Style" pegheads. Changing to a "Scroll Design" would add $ 10.00 to the price of the instrument. Any custom carving would be charged based on how involved I feel the time will be to carve it.
FRETBOARD/FINGERBOARD
Different builders often use these two terms somewhat interchangeably. To save cost/labor/time they also frequently use one piece of wood to accomplish both purposes. I prefer to use the terms in the following manner. The "Fretboard" is the piece that is glued to the soundboard. I find that a medium hard wood works best here to transmit the vibrations from the strings to the body. This piece also has the arch shaped cutouts. These limit the amount of fretboard that is in contact with the soundboard. Too much contact will dampen the ability of the soundboard to vibrate, thus deadening the tone and sound.
I call the thinner piece on top of this the "Fingerboard" and use a hard wood for it for a couple of reasons. First it holds the frets tighter, and because the strings are pressed against it, the harder wood will last longer than a softer wood. Usually I will inlay decorative dots either of a contrasting shade or mother-of-pearl at the first, third, fifth and "six and a half" frets. Not only are these decorative but they also help the player orient their finger positions.
ELECTRONICS
It is usually recognized that the mountain dulcimer is meant to be enjoyed by the person playing it. A small group of people in a quiet setting could also enjoy the music of the instrument. The fact is that the instrument does not have a very loud voice. This is most likely the reason you don't see mountain dulcimers in Bluegrass Bands. The old saying is that if you want loud dulcimer music, get a room full of them playing together!
I am often asked if the instrument could be fitted with an electronic pick-up so that it could be amplified. The quick answer is "yes" it is possible and some people have certainly done it. My standard answer is "no" I will not amplify my instruments. My desire is to honor and promote the old ways as much as I can and the old time dulcimers were simply not amplified.
There may well be a compromise for those that feel very strongly about amplification. There are pick-ups that attach to the exterior of the instrument but I can not attest to how well they work. Another option would be to simply put a mic on a stand close to the soundhole area of the insturment.